In order to produce raw silk cocoons are placed in a water bath. Using small brushes, the ends of the threads from several cocoons are grasped simultaneously and carefully wound. During the unwinding seven to eight silk threads, which are each several hundred meters long, are processed to form raw silk, the so-called Grège.
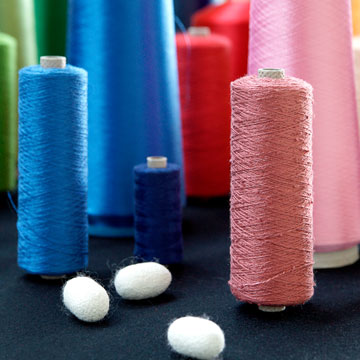
In a next step the raw material is twisted and dyed. In the process the sericin (silk gum) is removed. Only then does the silk acquire its characteristic shine and can be woven to create magnificent textiles. Silk for warp threads is called organzine, that for weft threads is called tram.
Defect cocoons, as well as further silk waste, form the starting material for floret silk, i.e. schappe silk. The short stapled raw product is spun at high speed to create thread, similar to the process used for wool or cotton.
In the 16th century Zurich began to manufacture floret silk. The raw material used was obtained from Lombardy. In the first half of the 19th century silk throwing experienced a great upsurge in the Canton of Zurich, however by the 1870s it had already entered a severe crisis.
Silk doubling mills, such as Zwicky in Wallisellen, which specialized, amongst other things, in the manufacture of sewing silk, survived through to the 20th century. To this day, the company Camenzind in Gersau on Lake Lucerne produces schappe silk.